Hydraulic Ball Valve: The Key to Efficient Fluid Control
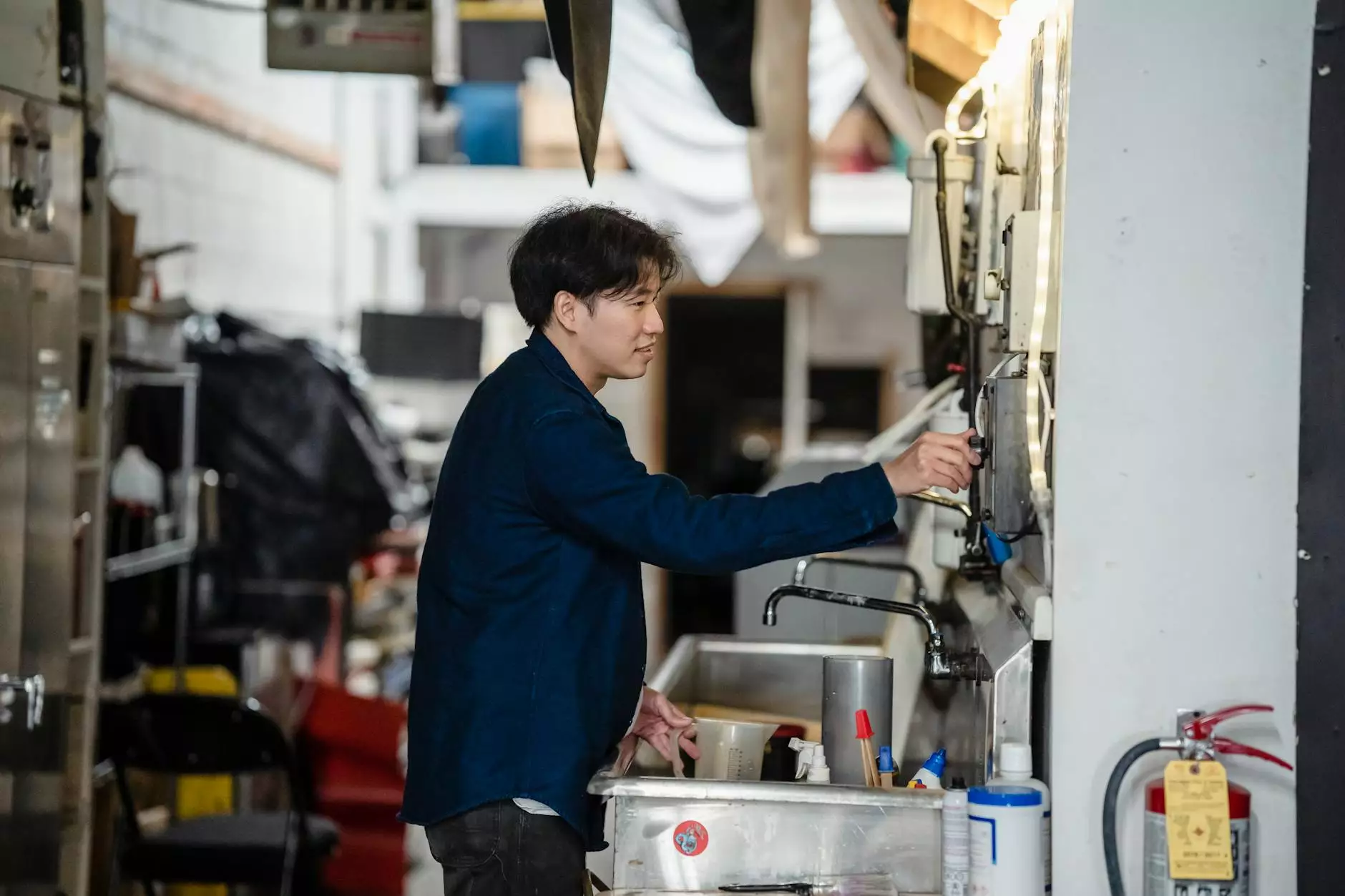
Hydraulic ball valves play a crucial role in the operation of fluid control systems across various industries. These valves offer excellent sealing capabilities, allowing for smooth and reliable operation even in demanding environments. This article dives deep into the world of hydraulic ball valves, exploring their features, benefits, applications, and maintenance practices to ensure they operate at their best.
Understanding Hydraulic Ball Valves
At their core, hydraulic ball valves are simple yet effective devices that serve to control the flow of liquids and gases. They consist of a hollow, perforated sphere—the ball—which can rotate within a valve body. When the ball’s hole is aligned with the flow direction, fluid can pass through; when it is perpendicular, the flow is shut off. This mechanism allows for quick and easy operation, making hydraulic ball valves a favorite in many industries.
Why Choose Hydraulic Ball Valves?
Choosing the right type of valve is critical for any fluid control system, and hydraulic ball valves offer several advantages:
- Durability: Constructed from robust materials such as stainless steel, brass, or PVC, hydraulic ball valves are built to withstand high pressure and temperature conditions.
- Leakage Prevention: The design of the ball and seat ensures a tight seal, reducing the risk of leakage, which is essential in hydraulic applications.
- Full Bore Design: Most hydraulic ball valves feature a full bore design that provides an unobstructed flow path, minimizing pressure drop and turbulence.
- Ease of Operation: They can be manually operated with a lever, or automated with electric or pneumatic actuators, providing flexibility in operation.
- Low Torque Requirements: This makes it easy to open or close the valve, reducing wear and tear on the operating mechanism.
Applications of Hydraulic Ball Valves
Hydraulic ball valves are versatile components used across a variety of industries due to their effective flow control capabilities. Some of the most common applications include:
1. Oil and Gas Industry
In the oil and gas sector, hydraulic ball valves are vital for controlling the flow of crude oil, natural gas, and other hydrocarbons. Their robust design allows them to operate reliably in high-pressure environments.
2. Water Treatment
These valves are commonly used in water treatment facilities to regulate the flow of water in various stages of purification and distribution, ensuring that systems operate efficiently and effectively.
3. Power Generation
In power plants, hydraulic ball valves are utilized to manage steam and water flows, optimizing the performance of turbines and cooling systems.
4. Chemical Processing
Due to their excellent sealing properties, hydraulic ball valves are extensively used in chemical processing to handle corrosive and hazardous fluids safely.
5. Food and Beverage Industry
In food processing, hygiene and safety are paramount. Hydraulic ball valves are used to control the flow of ingredients and ensure that systems adhere to safety regulations.
Key Features of Hydraulic Ball Valves
Several features make hydraulic ball valves stand out in the marketplace:
- Variety of Connections: They can be fitted with various connection types, including threaded, flanged, or welded ends, providing versatility for different applications.
- Different Materials: Available in various materials suited for specific applications, whether it’s corrosion resistance or temperature tolerance, ensuring that you find the right balance for your needs.
- Actuator Options: Hydraulic ball valves can be manually operated or equipped with pneumatic or electric actuators, allowing for automation which is vital for modern industrial processes.
- Position Indicators: Many models come with indicators that show the valve's position, making it easier for operators to monitor flow without needing to physically check the valve.
Selecting the Right Hydraulic Ball Valve
Choosing the right hydraulic ball valve can be overwhelming given the variety of options available. Here are some crucial factors to consider:
1. Application Requirements
Different applications have different requirements. Analyze the operational conditions including pressure, temperature, and the type of fluid being regulated. This information will guide you in selecting a valve that meets your needs.
2. Material Compatibility
The chosen material for the valve should be compatible with the fluid being transported. For instance, corrosive fluids require valves made of materials like stainless steel or specific plastic compounds. Ensure the valve's construction withstands potential corrosive interactions.
3. Pressure and Temperature Ratings
Each hydraulic ball valve will have specific pressure and temperature ratings. Be sure to choose a valve that can handle the maximum expected conditions of your application to ensure longevity and performance.
4. Size and Flow Rate
Valve size directly relates to the flow rate in a system. Use flow charts or hydraulic calculations to determine the appropriate valve size, ensuring that it can accommodate your operational requirements without causing excessive pressure drops.
Maintenance of Hydraulic Ball Valves
Regular maintenance extends the life of hydraulic ball valves and ensures reliable performance. Here are some maintenance tips to consider:
1. Visual Inspection
Conduct periodic visual inspections to detect any signs of leakage, corrosion, or damage. Check the seals and gaskets for wear and replace as necessary to prevent fluid loss.
2. Functional Testing
Regularly test the valve’s function to ensure it opens and closes correctly. This can involve operating the valve under normal working conditions to ensure it meets expected performance standards.
3. Lubrication
For manual ball valves, ensure that the operating handle is lubricated to reduce friction and wear. Follow manufacturer guidelines on appropriate lubricants.
4. Cleaning
Over time, debris can accumulate in and around valve components. Regular cleaning prevents blockages and ensures smooth operation. Be cautious about the cleaning agents to avoid damaging materials.
5. Professional Inspections
Consider using professional services for more in-depth inspections and maintenance, particularly for high-stakes applications where valve failure could result in significant operational issues or safety hazards.
Conclusion
In conclusion, hydraulic ball valves are indispensable components in a wide variety of fluid control applications. Their durability, reliability, and efficiency make them the preferred choice for industries ranging from oil and gas to food processing. By understanding their features, selecting the right products for specific applications, and adhering to proper maintenance practices, businesses can ensure optimal system performance. For high-quality fittings, including hydraulic ball valves, consider exploring the extensive offerings on fitsch.cn, your trusted source for fittings for sale.
Adopting the right hydraulic ball valve can make the difference between a well-functioning system and a costly failure. As industries continue to evolve, ensuring that your equipment is up to date, and well maintained will keep you ahead in today's competitive market. We hope this article has provided you with valuable insights into the world of hydraulic ball valves.