Electric Molding: The Future of Metal Fabrication
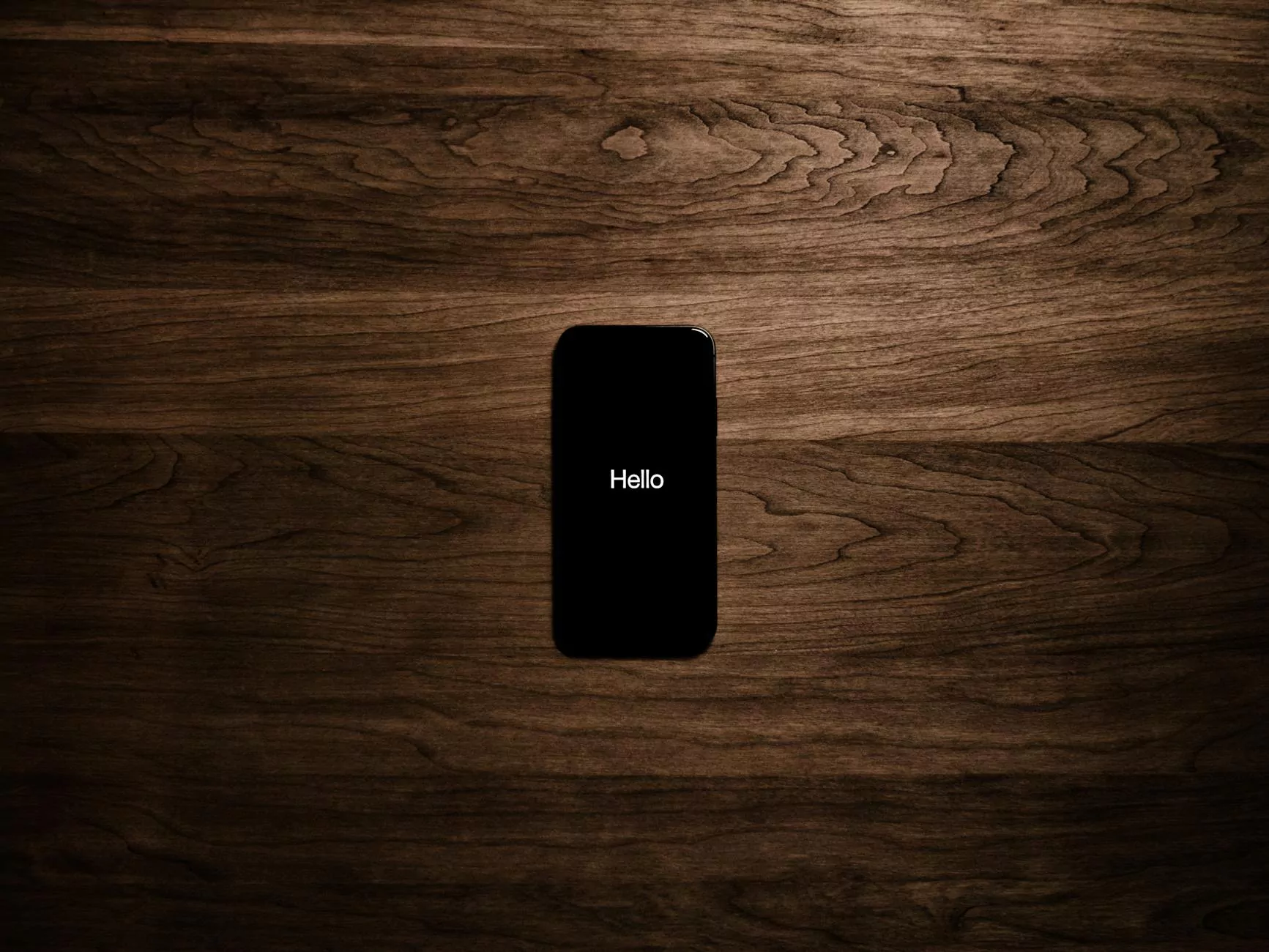
Electric molding represents a transformative force in the metal fabrication industry, redefining the ways manufacturers approach production processes. As we delve into the world of electric molding, it is imperative to understand its significance, applications, and the technological advancements that are reshaping this sector.
Understanding Electric Molding
At its core, electric molding is a process that utilizes electrical energy to shape and form materials, primarily metals, into desired configurations. This method is characterized by its efficiency, precision, and eco-friendliness compared to traditional molding techniques.
How Electric Molding Works
The fundamental principles of electric molding rely on controlled electrical currents and heat to manipulate materials. The process involves several key steps:
- Material Selection: Manufacturers begin by selecting appropriate metals or alloys suitable for the molding process.
- Heating Phase: The chosen material is heated using electrical energy until it reaches a malleable state.
- Forming Stage: The heated material is then shaped into molds that define its final structure.
- Cooling Process: Once formed, the material is cooled, solidifying its new shape.
Benefits of Electric Molding
Adopting electric molding techniques offers numerous advantages over traditional methods. Below are some key benefits:
1. Enhanced Precision
Electric molding allows for greater precision in the shaping process. The use of electronic monitoring systems ensures consistent heat distribution and material flow, resulting in components that meet stringent specifications.
2. Energy Efficiency
Compared to conventional molding techniques, electric molding is significantly more energy efficient. By minimizing heat loss and optimizing power usage, manufacturers can reduce operational costs while decreasing their environmental footprint.
3. Versatility
Electric molding is compatible with a wide range of metals and alloys, making it an adaptable solution for various industries, including automotive, aerospace, and electronics. The flexibility of this process allows manufacturers to cater to diverse customer needs.
4. Improved Material Properties
Utilizing electric molding can enhance the physical and mechanical properties of the molded components. The process can improve the grain structure of metals, leading to increased strength and durability.
Applications of Electric Molding in Metal Fabricators
The applications of electric molding in metal fabrication are vast and impactful. Below are some prominent areas where this technology shines:
Aerospace Industry
The aerospace sector demands components with exceptional strength-to-weight ratios and rigorous tolerances. Electric molding meets these requirements by producing lightweight yet robust structures essential for aircraft and spacecraft.
Automotive Manufacturing
In automotive production, electric molding enables the fabrication of intricate parts, such as engine components and body panels, that require high precision and consistent quality. This leads to improved performance and safety in vehicles.
Electronics Production
Electric molding is crucial for the electronics industry, where components like circuit boards and connectors must be manufactured with utmost precision. The reduced risk of defects translates to greater reliability in electronic devices.
Technological Advances in Electric Molding
The evolution of electric molding is accompanies by rapid technological advancements. Below are some cutting-edge innovations transforming the landscape:
Smart Monitoring Systems
Today’s electric molding machines are equipped with smart sensors that monitor temperature, pressure, and material properties in real time. These systems allow for immediate adjustments to ensure optimal molding conditions, further enhancing product quality.
Automated Production Lines
The integration of automation into electric molding processes enhances efficiency and throughput. Automated systems streamline production lines, reducing human error and ultimately lowering costs.
3D Printing and Hybrid Technologies
The convergence of electric molding with 3D printing technologies opens new avenues for complex designs and rapid prototyping. Hybrid systems allow manufacturers to combine the benefits of both techniques to create tailored solutions for unique challenges.
Conclusion: Embracing Electric Molding at deepmould.net
As the metal fabrication industry continues to evolve, embracing electric molding becomes essential for staying competitive. At deepmould.net, we are committed to leveraging the power of electric molding to deliver high-quality, innovative metal fabrication solutions that meet and exceed our clients’ expectations. With a focus on precision, efficiency, and sustainability, we are poised to lead the industry into a brighter, more effective future.
Get Started with Electric Molding Today
If you're interested in exploring how electric molding can benefit your business, contact us at deepmould.net. Our experts are ready to assist you in optimizing your metal fabrication processes.