Injection Molded Plastic Manufacturers: The Backbone of Modern Manufacturing
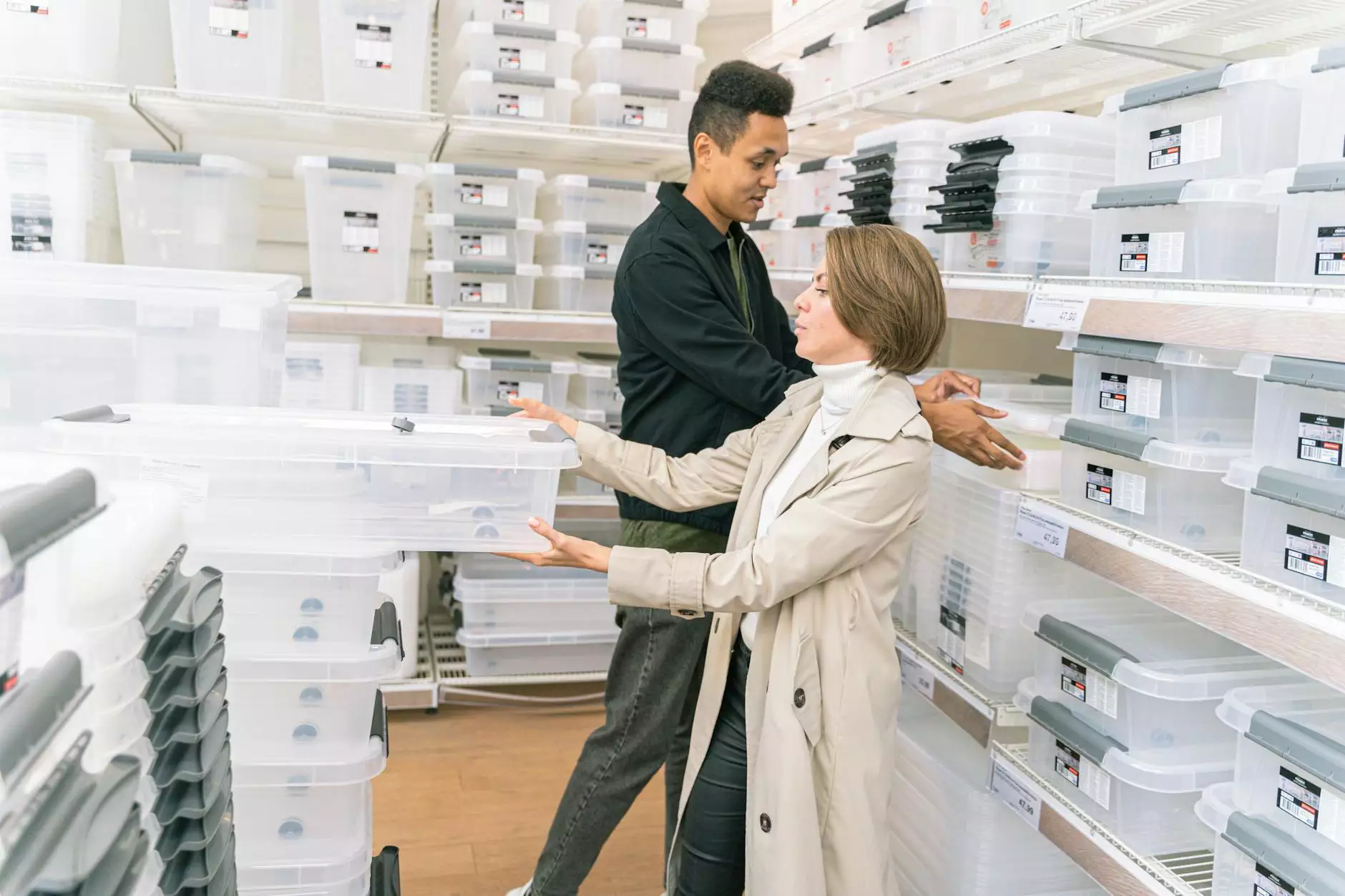
In today's fast-paced world, the role of injection molded plastic manufacturers cannot be overstated. These manufacturers are a vital component of numerous industries, providing essential products that enhance daily life and ensure business efficiency. This article delves into the details of injection molding, the benefits it offers, and how to choose the right manufacturer for your needs.
What is Injection Molding?
Injection molding is a manufacturing process where molten plastic is injected into a mold cavity, forming the desired shape as it cools and solidifies. This process is widely used for producing a variety of plastic parts, from intricate designs to simple containers.
Key Components of Injection Molding
- Mold: The mold is a hollow metal block that defines the shape of the final product. Creating a mold involves precision engineering and can be expensive, but it is essential for high-volume production.
- Injection Unit: This component melts the plastic pellets and injects them into the mold. It is crucial for maintaining temperature and ensuring the proper flow of material.
- Clamping Unit: This unit holds the mold together during the injection process, preventing any leakage of the molten material.
The Process of Injection Molding
The process of injection molding can be broken down into several key steps:
1. Designing the Mold
The first step is designing a mold that will produce the desired shape. This involves computer-aided design (CAD) software to create precise drawings and specifications.
2. Material Selection
Choosing the right type of plastic is crucial, as different plastics have varying properties and applications. Common choices include:
- Polyethylene: Lightweight and flexible, often used for packaging.
- Polypropylene: Known for its durability and resistance to chemicals, commonly used for automotive parts.
- Polystyrene: Clear and brittle, used for disposable containers and packaging.
3. Melting and Injection
Once the material is selected, it’s fed into the injection unit, where it is heated until it becomes molten. The molten plastic is then injected into the mold under high pressure.
4. Cooling and Ejection
After injection, the molten plastic cools and solidifies. Once it reaches the proper temperature, the mold opens to eject the finished product.
5. Finishing Touches
Finally, any necessary finishing processes, like trimming, surface treatments, or additional assembly, are conducted to ensure the product meets quality standards.
Benefits of Working with Injection Molded Plastic Manufacturers
Partnering with experienced injection molded plastic manufacturers offers numerous advantages, including:
Cost Efficiency
One of the most significant benefits of injection molding is the reduced cost per unit when producing large quantities. The initial investment in mold design and manufacturing might be high, but the long-term savings are substantial.
Precision and Quality
Injection molding produces parts with high dimensional accuracy and consistency. This is essential for industries that require tight tolerances and high-quality finishes.
Versatility
The injection molding process can produce a wide range of products, from small components to large housings, making it a flexible choice for various applications such as:
- Consumer Goods
- Automotive Parts
- Industrial Equipment
- Medical Devices
Complex Geometries
Injection molding allows for the creation of intricate designs and complex geometries that would be difficult, if not impossible, to achieve with other manufacturing methods.
How to Choose the Right Injection Molded Plastic Manufacturers
Selecting the right manufacturer is critical to your project's success. Here are some key factors to consider:
Experience and Expertise
Look for manufacturers with a proven track record in injection molding. Their expertise will positively impact the quality of your final products.
Technology and Equipment
Examine the technology and equipment used by the manufacturer. State-of-the-art machinery can enhance efficiency, precision, and the range of materials they can process.
Quality Assurance Processes
Ensure that the manufacturer has robust quality assurance processes in place to monitor and maintain the standards of production.
Customization Capabilities
Every project has unique requirements. Choose a manufacturer that offers customization options, from design changes to material selection.
Industry Applications of Injection Molding
The versatility of injection molding means it is utilized across numerous industries. Here are a few sectors that greatly benefit from the capabilities of injection molded plastic manufacturers:
Automotive Industry
In the automotive sector, injection molding is used for components such as dashboards, interior trim, and various plastic housings. The ability to produce lightweight and durable parts enhances vehicle efficiency.
Consumer Electronics
Consumer electronic products often require high-quality components that are both aesthetically pleasing and functional. Injection molded parts, such as casings and buttons, are extensively used.
Medical Devices
The medical industry relies on injection molding to produce components used in medical devices, like syringes, inhalers, and surgical instruments, where precision and sterility are paramount.
Packaging
Plastic packaging solutions are ubiquitous, and injection molding provides a vast range of products, including bottles, containers, and blister packs that are both practical and visually appealing.
Challenges Facing Injection Molded Plastic Manufacturers
Despite the advantages, injection molded plastic manufacturers face several challenges:
Material Costs
Fluctuations in the prices of raw materials can impact production costs. Manufacturers must strategize to mitigate these risks, possibly by securing long-term contracts with suppliers.
Environmental Concerns
The use of plastics raises environmental issues. Manufacturers are increasingly focusing on sustainable practices, such as using biodegradable materials and recycling post-production scraps.
Technological Advancements
Keeping pace with technological developments requires continuous investment in equipment and training. Manufacturers must remain adaptable to leverage new techniques and materials.
The Future of Injection Molding
As technology progresses, the future of injection molding looks promising. Innovations such as:
- 3D Printing: Used for rapid prototyping and even for creating molds in some cases.
- Smart Manufacturing: Integrating IoT devices for efficient monitoring and quality control.
- Advanced Materials: The development of new plastics that are stronger, lighter, and more sustainable.
Conclusion
Understanding the role and capabilities of injection molded plastic manufacturers is crucial for any business looking to utilize plastic parts effectively. Their ability to provide high-quality, cost-effective solutions while adapting to market demands is indispensable. By choosing the right manufacturer, you can ensure that your products meet the highest standards of quality and innovation, paving the way for business success.
Whether you are in the automotive sector, consumer goods, or any other industry, collaborating with experienced manufacturers like Deep Mould can elevate your projects and streamline your production processes. Embrace the future of manufacturing by harnessing the potential of injection molding today.