Understanding the Role of a Plastic Injection Mold Maker
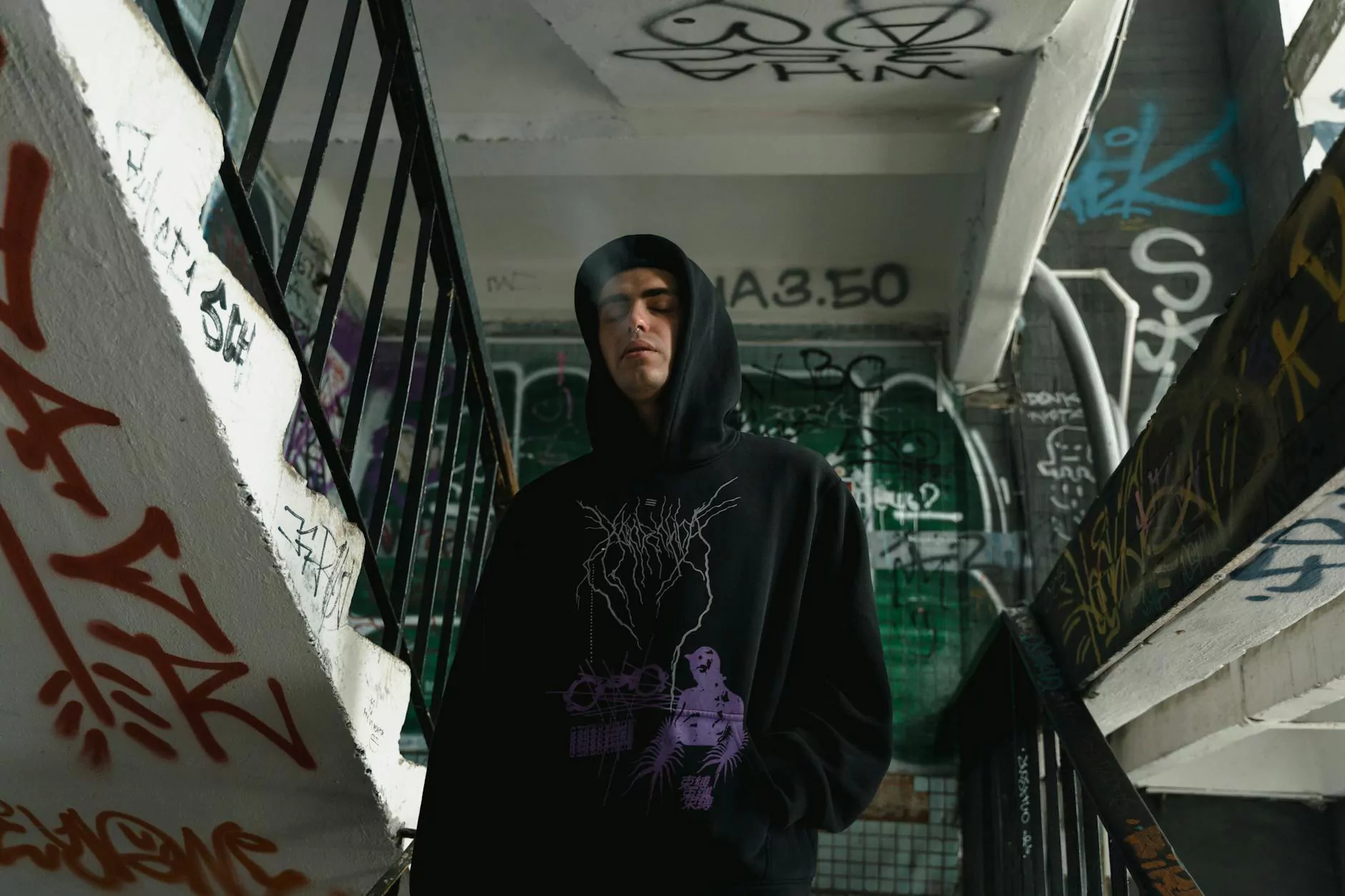
The world of manufacturing is vast, and within it exists the specialized field of plastic injection mold making. These artisans are pivotal in producing high-quality plastic components that meet the demands of various industries. This article dives deep into the intricacies of the role of a plastic injection mold maker, exploring processes, benefits, and why they are essential in today’s manufacturing landscape.
What is a Plastic Injection Mold Maker?
A plastic injection mold maker is a highly skilled professional who designs, fabricates, and maintains molds used for plastic injection molding. This process involves injecting molten plastic into a mold to create parts and products of specific designs. The precision and expertise required in this role are critical for ensuring high-quality output and consistency in production.
The Plastic Injection Molding Process
The process of plastic injection molding is sophisticated, consisting of several key steps:
1. Mold Design
The journey begins with designing the mold. This stage involves the use of computer-aided design (CAD) software to create a detailed mold blueprint. The design must consider the product specifications, material characteristics, and production volume.
2. Material Selection
Choosing the right type of plastic is crucial, as it impacts the quality, durability, and performance of the final product. Common materials include:
- Polypropylene (PP)
- Polyethylene (PE)
- Polystyrene (PS)
- Polyvinyl Chloride (PVC)
- Acrylonitrile Butadiene Styrene (ABS)
3. Mold Fabrication
With designs in hand and materials selected, the actual fabrication of the molds begins. This step involves:
- Machining: Using CNC machines to create precise mold components.
- Assembly: Bringing together all parts to form a functional mold.
- Testing: Conducting trial runs to ensure the mold operates correctly.
4. Injection Molding
Once the mold is ready, it is placed into an injection molding machine, where plastic pellets are heated until they melt. This molten plastic is then injected into the mold at high pressure, allowing it to fill every detail before cooling and solidifying. The final phase involves the ejection of the molded part from the mold.
The Importance of a Skilled Plastic Injection Mold Maker
A skilled plastic injection mold maker brings numerous benefits to the manufacturing process:
Precision and Accuracy
With an understanding of the material properties and the intricacies of mold design, they ensure that every component meets the exact specifications and tolerances required by the customer.
Cost Efficiency
By producing high-quality molds that last longer and require less maintenance, a proficient mold maker contributes to significant cost savings in production.
Faster Time to Market
With efficient design and fabrication processes, a knowledgeable mold maker can help businesses bring their products to market faster, gaining competitive advantage.
Qualities to Look for in a Plastic Injection Mold Maker
Choosing the right plastic injection mold maker for your business is paramount. Here are essential qualities to consider:
Experience and Expertise
Look for a mold maker with a proven track record in the industry. Their experience will guide them through potential challenges and ensure high-quality results.
Advanced Technology Utilization
The use of cutting-edge technology, such as 3D printing and high-precision CNC machining, allows mold makers to produce superior molds effectively.
Strong Communication Skills
A productive working relationship relies on open communication. Your mold maker should understand your needs and provide feedback throughout the process.
The Future of Plastic Injection Molding
The industry is evolving, driven by advancements in technology and an increased emphasis on sustainability. Key trends include:
1. Adoption of Sustainable Practices
Many companies are moving towards using biodegradable materials and recyclable plastics, reducing the environmental impact of molded products.
2. Integration of Automation
Robotic systems and automated processes are becoming more commonplace, enhancing the speed and efficiency of production.
3. Customization and Small Batch Production
With advancements in technology, low-cost, customized production is increasingly viable, catering to specific consumer demands without sacrificing quality.
Conclusion: Partnering with a Reliable Plastic Injection Mold Maker
In conclusion, the expertise of a plastic injection mold maker is invaluable in the manufacturing sector. Their role ensures the production of high-quality plastic components, driving efficiency and innovation. By selecting the right partner, businesses can harness the full potential of plastic injection molding, remaining competitive in an ever-evolving market.
For more information on finding a reliable mold maker, or to explore further into the realm of metal fabricators, visit deepmould.net. Your journey into efficient manufacturing starts here!